I am facing this problem, which is causing the two push-pull MOSFET to extreme stresses.
I am using this to power TAS5630 amp. the boost converter is converting the 12V DC voltage to 36V DC (unregulated). As this is a car amplifier so the battery voltage can be 10V to 14.5V.
Everything is ok upto 13.5V DC input. But when the input voltage is higher than that, inductive spike is seen at the MOSFET drain and they becomes hot.
At 13.8V or higher the kick exceeds the max Vds 40V and the FETs are starting to runaway.
I have attached some screenshot and unsnubbed oscillation at MOSFET drain. Please help me to remove the inductive kick @15V.
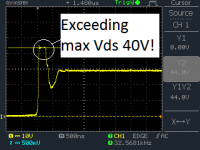
View attachment test waveform.zip
I am using this to power TAS5630 amp. the boost converter is converting the 12V DC voltage to 36V DC (unregulated). As this is a car amplifier so the battery voltage can be 10V to 14.5V.
Everything is ok upto 13.5V DC input. But when the input voltage is higher than that, inductive spike is seen at the MOSFET drain and they becomes hot.
At 13.8V or higher the kick exceeds the max Vds 40V and the FETs are starting to runaway.
I have attached some screenshot and unsnubbed oscillation at MOSFET drain. Please help me to remove the inductive kick @15V.
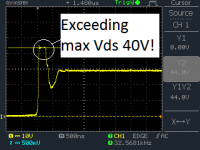
View attachment test waveform.zip